Tokyo, Japan, March 15, 2024 – Toray Industries, Inc., announced today that it has developed an insulating resin material for hybrid bonding (micro bonding). The material is based on Semicofine™ and Photoneece™. These are high-heat-resistant polyimide coatings for semiconductor and display devices. The new material combines a conventional polyimide coating agent with the company’s processing and bonding technologies. It can enhance the yields and reliability of semiconductor devices in the hybrid bonding process, which entails bonding semiconductor chips with metal electrodes. Toray will push ahead with prototyping and providing samples to customers. It aims to obtain materials certification in 2025 and start mass production by 2028.
A leading high-performance packaging technology applied in recent years is three-dimensional (3D) packaging. This process involves vertically stacking semiconductor chips (see Figure 1). Hybrid bonding is
particularly promising for high-performance semiconductor chips requiring fine structures with bump pitches (the spacing between adjacent electrodes joined by solder) of 10 microns or less.
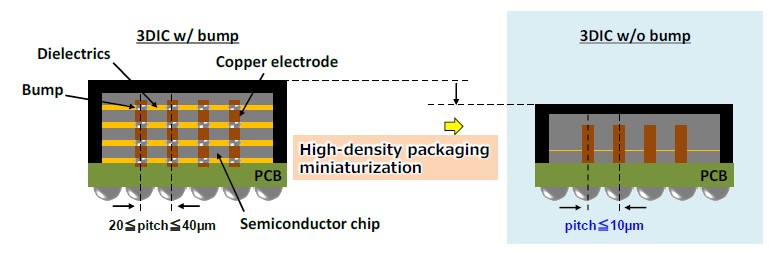
schematic diagram of 3D mounting packages
Toray markets resin bonding materials for 3D chip-to-chip packaging with fine bump pitches of about 20 microns. Hybrid bonding differs from conventional 3D packaging because it entails directly joining metal electrodes without using bumps, making it possible to further shorten electrode pitches.
In hybrid bonding, the chip-to-wafer technique has attracted considerable attention for high-density
packaging of different types of chips. This technique involves processing one wafer substrate to the chip
size and bonding it to another wafer substrate. Silicon dioxide and other inorganic materials are usually
used as insulating materials for hybrid bonding. There are two key challenges, however, with applying the
chip-to-wafer technique. The first is that silicon dust generated in chip dicing can be trapped during hybrid
bonding, causing chip bonding defects and lowering yields. The second is that trapped silicon dust
threatens the reliability of semiconductor packages (Figure 2).
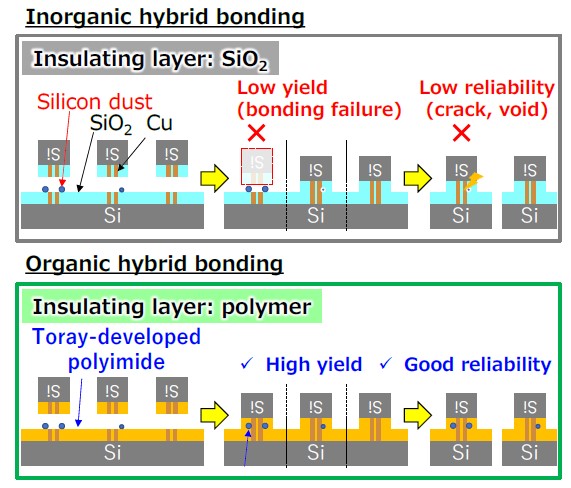
Since 2020, Toray has carried out hybrid bonding experimental demonstrations with the Institute of Microelectronics, a semiconductor research unit of Singapore’s Agency for Science, Technology and Research. This work has tapped the company’s accumulated expertise in functional plastics design technology in employing sophisticated molecular design and pursues excellence to create insulating polymers offering high heat resistance and excellent mechanical properties (Figure 3).
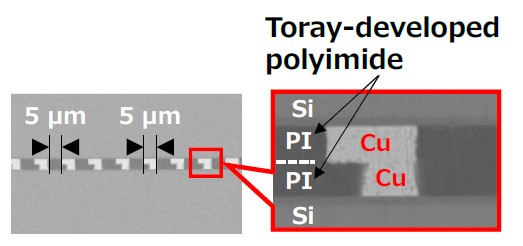
By collaborating with that entity and various semiconductor-related companies, Toray looks to apply this material to chip-to-wafer hybrid bonding. It seeks to boost the yields and reliability of chiplets and make it possible to integrate differing chips in a single package.
Toray will incorporate its new material in its lineup of resin products for semiconductor devices and electronic components with a view to fostering the adoption of high-performance next-generation semiconductor packages for high-speed communications devices and server applications. Toray will keep leveraging its core technologies of synthetic organic and polymer chemistry, biotechnology, and nanotechnology to innovate materials in keeping with its commitment to delivering new value and contributing to social progress.
For more information, please visit our website at www.toray.com