January February 2025
Volume 29, Number 1
There have been any number of market drivers for advanced semiconductor packaging over the years, including improved form factor, power, and operational temperature requirements to accommodate the demand for ever-smaller consumer electronics. Automotive applications have also been a significant driver for packaging. More recently, the semiconductor industry is embracing the process improvements needed to implement artificial intelligence in a broad swath of military and commercial applications. The cover article discusses an integrated wet processing platform that meets the needs of chips for AI applications, and that also has a low cost of ownership.
Cover image courtesy of iStock/Pony Wang
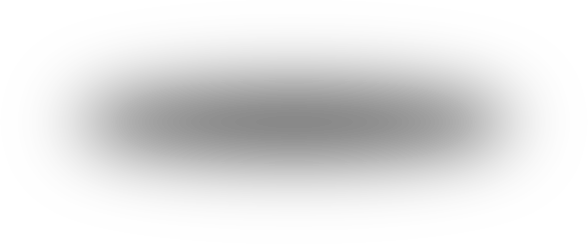
March April 2025
Volume 29, Number 2
Advanced packaging substrates, such as glass-based interposers combined with automated packaging processes, can overcome manufacturing bottlenecks in photonic component assembly. This approach will enable photonic and electronic co- packaged subsystems to scale to large-volume production. As a result, mass market demands--including data center communications, artificial intelligence, sensing and diagnostics—will be addressed. The cover image shows the packaging of a microlens array to a flip-chip assembled InP photonic integrated circuit on a glass electrical
interposer with BGA contacts.
Cover photo courtesy of Tyndall National Institute
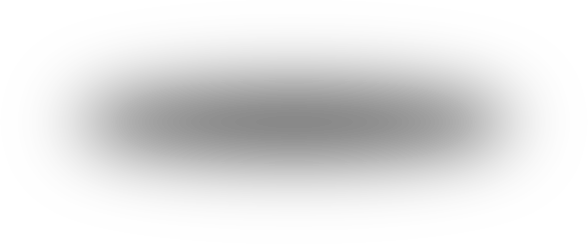
May June 2025
Volume 29, Number 3
The growing size of AI clusters is pushing data centers to their physical limits, necessitating the development of multi-site AI clusters to distribute workloads. These clusters rely on coherent ZR optics for high-speed data transfer, which is why it is imperative to increase the yield of such cutting-edge optical modules. This increase in yield can be enabled by using efficient PIC testing.
.
Cover image courtesy of iStock/Quantico69
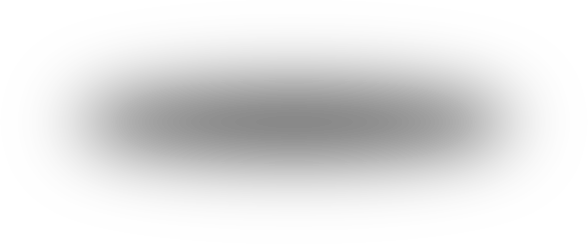
July August 2025
Volume 29, Number 4
To meet the demand for extreme interconnection density reduction, a holistic approach is needed to handle the challenges of overlay requirements. Combining advanced front-end lithography with state-of-the-art bonding equipment achieves this objective. The cover article also discusses how what is learned with respect to tackling overlay challenges can also be used to enable advanced packaging, bonding-assisted 3D stack engineering for thermal management, and D2W hybrid bonding applications.
.
Cover image courtesy of iStock/koto feja
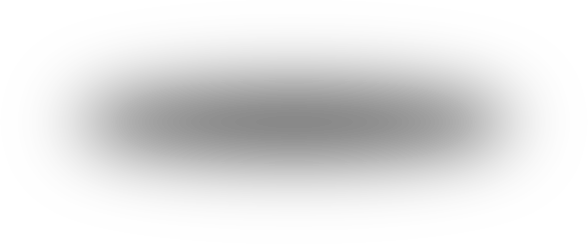